Table of Contents
ToggleConcrete block manufacturing in Florida is a booming industry that provides high quality building materials to construction contractors for their projects.
In the world of construction, the foundation of any project lies in the quality of the materials used.
One essential material that is often overlooked but crucial to the success of a project is concrete blocks.
These building blocks play a significant role in the structural integrity and durability of a construction project.
Let’s explore the world of concrete block manufacturing in Florida and how it can benefit construction contractors.
The Foundation of Concrete Block Manufacturing in Florida
At the core of concrete blocks manufacturing lies a process steeped in precision and expertise.
This industry, particularly vibrant in Florida, hinges on the creation of precast concrete blocks, pivotal for myriad construction endeavors.
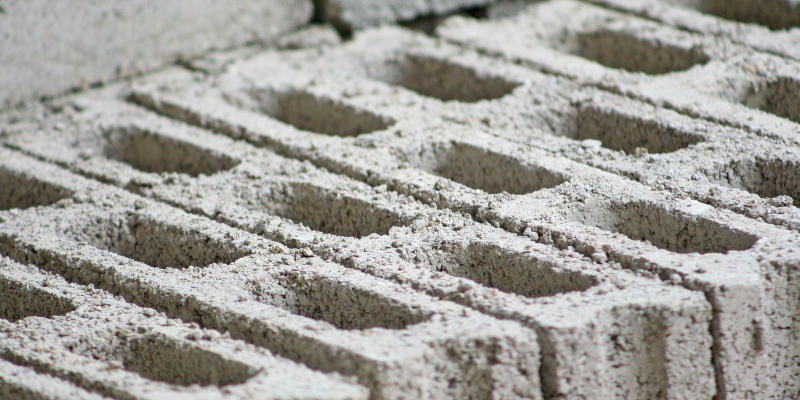
The manufacturing sequence begins with a carefully calibrated blend of cement, aggregate, and water.
This mixture is the backbone of concrete block production, where the correct proportions are critical for achieving the desired strength and durability of the blocks.
The concoction is then poured into meticulously designed molds.
These molds dictate the shape and size of the concrete blocks, allowing for a range of specifications to be met with precision.
The next stage—curing—is where the mixture solidifies, transforming into the sturdy blocks that will eventually contribute to the structural integrity of various buildings and structures.
This curing process is a delicate balance of time and conditions, ensuring that the blocks attain optimum hardness and resilience.
Once the curing phase concludes, the blocks are extracted from the molds, a moment that marks their readiness to be integrated into construction projects.
This streamlined process, from mixing to molding to curing, underscores the importance of precision in every step to guarantee the production of high-quality concrete blocks.
It’s this meticulous approach to manufacturing that enables contractors in Florida and beyond to rely on these blocks for their construction needs, laying the groundwork for structures that stand the test of time.
Key Factors Affecting the Quality of Concrete Blocks
The integrity and durability of concrete blocks are influenced by several critical factors that determine their suitability for construction projects.
A paramount aspect is the proportion of materials used in the mixture—specifically, the cement-to-aggregate ratio.
This balance affects the strength and density of the final product, making it essential for manufacturers to adhere to precise formulations.
Additionally, the quality of the raw materials plays a significant role.
High-grade cement and aggregates ensure that the blocks possess the requisite durability for structural applications.
Contaminants or substandard materials can compromise the integrity of the blocks, leading to potential issues in construction projects.
Another crucial factor is the curing process, which directly impacts the block’s strength and moisture content.
Proper curing ensures that the blocks develop the desired hardness and are less susceptible to environmental damage over time.
The environment in which the blocks are cured, including temperature and humidity levels, must be carefully controlled to achieve optimal results.
Techniques used in the manufacturing process also contribute to the block’s quality.
Modern manufacturing facilities employ state-of-the-art equipment and processes to ensure uniformity in size, shape, and density of the blocks, which are essential for ease of use in construction and the overall aesthetic of the completed structure.
Understanding and optimizing these factors are essential for concrete block manufacturers, especially in a competitive market like Florida, to provide products that meet the high standards required by construction contractors.
Navigating the Challenges of Large-Scale Projects
Tackling large-scale construction projects requires a strategic approach to overcome inherent complexities, such as securing a steady supply of materials and coordinating logistics across multiple teams.
One of the pivotal steps to ensure smooth execution is partnering with a dependable concrete blocks supplier.
This alliance not only guarantees a consistent supply of high-quality blocks but also streamlines the procurement process, reducing potential delays and budget overruns.
A key advantage of such a partnership includes the ability to leverage the supplier’s expertise in logistics and inventory management, ensuring that the right quantity of blocks is delivered at the right time, thereby minimizing storage costs and space requirements on-site.
Furthermore, a supplier with a robust distribution network can adapt to the dynamic needs of a large project, providing flexible delivery schedules and even accommodating last-minute changes.
This level of reliability and flexibility from a supplier is instrumental in managing the intricacies of large-scale projects, enabling contractors to focus on the critical aspects of construction and project management without the added stress of material shortages or logistical setbacks.
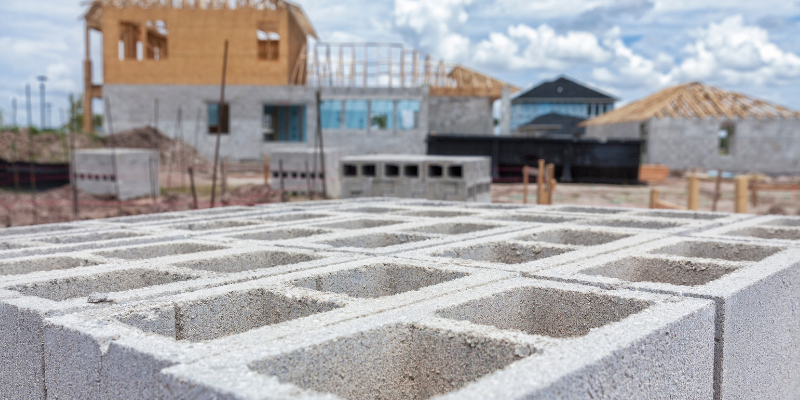
How to Choose a Reliable Concrete Blocks Supplier
Selecting a dependable supplier of concrete blocks requires a strategic approach that goes beyond just comparing prices.
First and foremost, evaluate the supplier’s industry standing and longevity.
Concrete block manufacturing companies that have been successfully operating for years are often more reliable and possess a deeper understanding of the market dynamics.
They are likely to have refined their manufacturing processes to deliver products that consistently meet or exceed standards.
Another critical factor to consider is the supplier’s capacity to fulfill orders of varying sizes, especially for large-scale projects.
This ensures that your project’s demands can be met without unnecessary delays.
Delve into the supplier’s track record of timeliness and ability to maintain quality under tight deadlines.
Certifications and quality assurances are also paramount.
Suppliers who adhere to recognized standards and possess certifications such as ISO provide an added layer of confidence in their products.
This not only speaks to the quality of the concrete blocks but also to the company’s commitment to maintaining high industry standards.
Engage with the supplier’s existing clients to gather feedback on their experience, focusing on aspects such as customer service, problem resolution, and overall satisfaction.
This direct feedback can provide invaluable insights into what you might expect in terms of service and support.
Lastly, assess the supplier’s commitment to innovation and sustainability.
A partner who invests in advanced manufacturing technologies and sustainable practices is not only beneficial for the environment but also indicative of a forward-thinking company that is likely to deliver superior products and services.
By carefully considering these factors, construction contractors can form a partnership with a concrete block supplier that enhances the success of their projects in Florida.
Innovations in Concrete Block Manufacturing in Florida
The concrete blocks manufacturing in Florida industry is witnessing a transformative phase, marked by technological advancements and innovative methodologies that are setting new benchmarks for quality and efficiency.
Key among these innovations is the adoption of automated production lines.
These automated systems streamline the manufacturing process, from mixing to molding to curing, significantly reducing labor costs and production time while enhancing consistency across batches.
Another groundbreaking development is the use of advanced curing techniques, such as accelerated curing methods that employ steam or heat to expedite the hardening process.
This not only shortens the production cycle but also improves the blocks’ strength and durability.
Furthermore, the industry is exploring the incorporation of sustainable materials into the production mix.
The use of fly ash, a byproduct from coal combustion, as a partial replacement for cement, is gaining traction.
This not only recycles waste material but also reduces the carbon footprint of the manufacturing process.
Additionally, lightweight aggregates are being investigated to reduce the weight of concrete blocks, making them easier to handle and decreasing transportation costs.
These innovations are reshaping the landscape of concrete blocks manufacturing, offering enhanced solutions that meet the evolving demands of the construction industry.
The Environmental Impact of Concrete Blocks Production
In the quest for sustainability within the concrete blocks production industry, a critical examination of environmental implications has become increasingly pertinent.
Manufacturers are adopting green practices, including the utilization of recycled materials such as fly ash and slag, which not only helps in managing industrial waste but also reduces the reliance on virgin materials, thereby conserving natural resources.
Innovations like these play a significant role in diminishing the carbon footprint associated with the manufacturing process.
Energy efficiency is another area of focus, with state-of-the-art facilities optimizing machinery and processes to lower energy consumption.
Furthermore, the exploration of lightweight aggregates is contributing to reduced transportation emissions, as lighter blocks mean fewer trips and lower fuel usage.
These initiatives illustrate a growing commitment among producers to not only meet the demand for durable building materials but also to ensure that the production of concrete blocks advances in harmony with environmental stewardship.
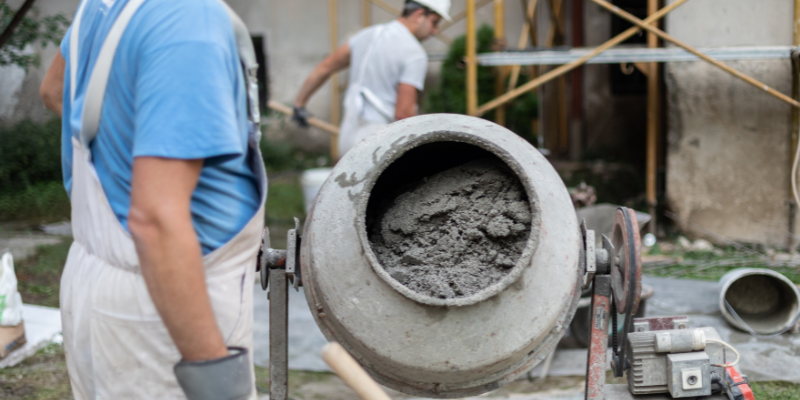
Case Studies: Successful Projects Using High-Quality Concrete Blocks
Examining successful projects that utilized high-quality concrete blocks illuminates the tangible benefits these materials bring to construction endeavors.
For instance, a notable commercial development in Miami leveraged superior concrete blocks, leading to a structure that excelled in both durability and aesthetic appeal.
This choice allowed for faster construction timelines and significant cost efficiencies, showcasing the strategic advantage of partnering with top-tier concrete block suppliers.
Another example includes a residential complex in Orlando, where the use of high-quality blocks ensured enhanced insulation properties, reducing long-term energy costs for inhabitants.
These projects exemplify how the careful selection of concrete blocks can positively impact the outcome of construction projects, underlining the importance of quality materials in achieving excellence in the built environment.
Concrete block manufacturing in Florida is a booming industry that not only directly impacts our state’s economy, but also our environment and way of living.