Table of Contents
ToggleUnderstanding how concrete blocks are made is essential for anyone involved in construction, whether you’re managing large projects or simply seeking reliable construction suppliers.
Concrete blocks are a staple in the construction industry, valued for their durability, strength, and versatility.
In this blog post, we will walk you through the entire manufacturing process of concrete blocks, detailing each step and the importance of maintaining high standards.
According to Powerblanket.com, the global concrete blocks and bricks market was valued at USD 350.80 billion in 2021.
The Essential Raw Materials Required for Concrete Blocks
Concrete blocks owe their strength and durability to a precise blend of raw materials: cement, aggregates, water, and additives.
Cement serves as the binding agent, conferring the necessary structural integrity.
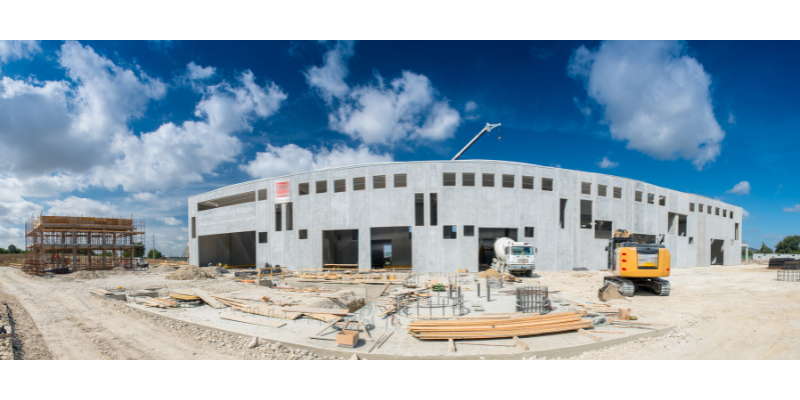
Aggregates, ( sand, gravel, or crushed stone ) are crucial in how concrete blocks are made and contribute to the thermal and mechanical properties.
The choice and quality of these aggregates are crucial, impacting everything from density to thermal performance.
Water is indispensable for hydrating the cement and achieving the correct mixture consistency.
Additionally, specialized additives can be introduced to enhance workability, adjust setting times, or improve resistance to environmental stressors.
How Concrete Blocks are Made: The Mixing Process
Achieving the right mix consistency is paramount for manufacturers of concrete blocks.
The raw materials—cement, aggregates, water, and any required additives—are introduced into a mixer.
Depending on the production scale, this mixer could be a batch or continuous type.
The proportion of materials is meticulously calculated, usually one part cement, two parts sand, and four parts gravel.
Water and additives are also measured with precision to ensure the mixture is neither too dry nor too wet.
The mixing process aims to create a homogeneous, paste-like consistency.
This consistency is crucial, allowing the mixture to be molded into blocks while maintaining structural integrity.
The Molding Stage: Shaping Concrete into Blocks
Once the mix reaches the ideal consistency, it’s time for the molding stage, where the concrete is formed into blocks.
The prepared concrete is transferred into molds, typically made of steel or plastic.
These molds are designed in various shapes and sizes to produce different types of blocks, including standard, hollow, and insulated variants.
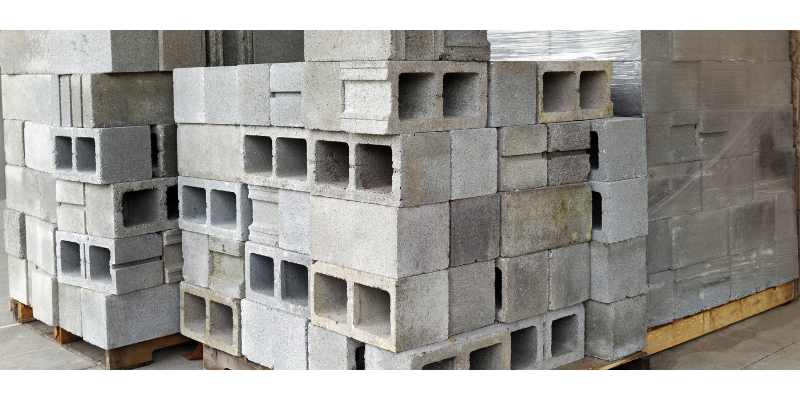
The molds are filled with the concrete mix, which is then vibrated or compacted to eliminate air pockets and ensure an even distribution.
This step is vital for achieving uniform density and optimal strength.
The vibrating or compacting process ensures that every part of the block is thoroughly filled, leaving no voids or weaknesses.
Depending on the design, and how the concrete blocks are made, there may be voids to reduce weight and improve insulation properties.
This meticulous molding process lays the foundation for the quality and durability of the finished concrete blocks, making it a critical phase in their production.
The Curing Process: Strengthening the Concrete Blocks
Curing is indispensable to the development of concrete blocks, dictating their final strength and durability.
As soon as the blocks are molded, the curing phase commences, spanning from several hours to days, depending on the method utilized:
- Air curing: Relies on a controlled environment to retain moisture, essential for the hydration process.
- Steam curing: Favored for mass production, accelerates strength development by exposing the blocks to steam in a regulated manner.
- Water curing: On the other hand, involves maintaining the blocks in a damp condition to ensure continuous hydration.
Each method requires meticulous attention to environmental conditions, such as temperature and humidity, to foster optimal curing.
Quality Control: Ensuring High Standards in Block Production
Quality control is an indispensable aspect of concrete block production, ensuring that each unit meets stringent industry standards and is suitable for use in construction.
The process begins even before the manufacturing kicks off, with rigorous testing of raw materials like cement, aggregates, and water for quality and consistency.
These initial tests are crucial in maintaining the integrity of the mix throughout the production cycle.
During the mixing phase, samples are periodically taken to confirm that the proportions of cement, aggregates, water, and any additives align with the predetermined formula.
Deviations, however small, can significantly impact the block’s final properties, making this step critical for quality assurance.
Post-molding, as the blocks undergo curing, further evaluations are conducted.
Cured blocks are subjected to a battery of tests to verify their compressive strength, dimensional accuracy, and overall appearance.
Compressive strength tests ensure that the blocks can withstand structural loads, a key requirement for their use in construction.
Dimensional checks confirm that the blocks conform to specified size tolerances, while visual inspections catch any surface imperfections that might affect the block’s performance or aesthetic appeal.
Each stage of this quality control process is meticulously documented, creating a traceable record that manufacturers can refer to for compliance and improvement.
This rigorous approach not only minimizes defects but also fosters confidence in the end-users, ensuring that the concrete blocks will perform reliably in various construction scenarios.
Storage and Transportation: Protecting the Finished Blocks
Proper storage and transportation are crucial to maintaining the integrity of finished concrete blocks.
Once the blocks have successfully passed through the curing and quality control stages, they need to be carefully handled to avoid any damage that could compromise their structural reliability.
Blocks are typically stacked in uniform rows on sturdy pallets, allowing for adequate air circulation.
This arrangement is not only practical for storage but also ensures that the blocks remain in optimal condition.
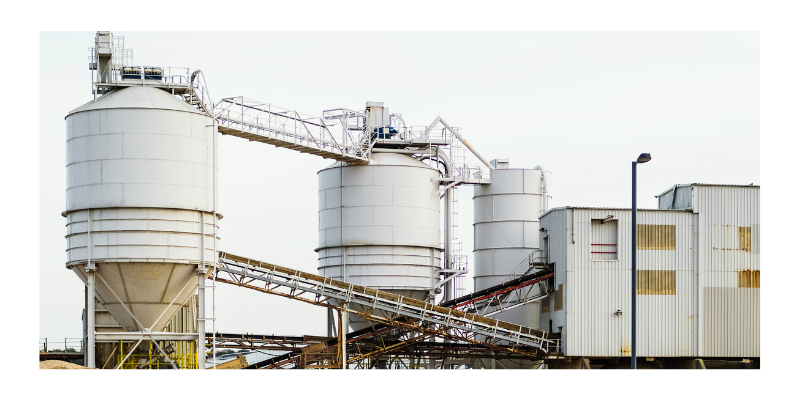
The storage area itself should be free from excessive moisture and shielded from extreme weather conditions.
Such measures prevent moisture absorption, which can adversely affect the blocks’ performance over time.
When transporting these blocks to construction sites, using the right type of vehicle is vital to minimize movement and potential damage.
Securing the blocks properly during transit is equally important; straps or other securing methods can be employed to prevent any shifting.
Drivers should be well-trained to handle these loads carefully, and routes should be planned to avoid any undue stress on the cargo.
Timely and efficient transportation also ensures that project schedules remain on track, allowing contractors to proceed without delays.
By paying attention to these storage and transportation details, you can maintain the high quality of the concrete blocks from the factory floor to the construction site.