Table of Contents
ToggleAs a construction contractor in Florida, sourcing high-quality materials is crucial to the success of your projects.
When it comes to concrete blocks, finding reliable suppliers can be a challenge.
In this blog post, we will explore the ins and outs of navigating the field of concrete block suppliers for Florida contractors.
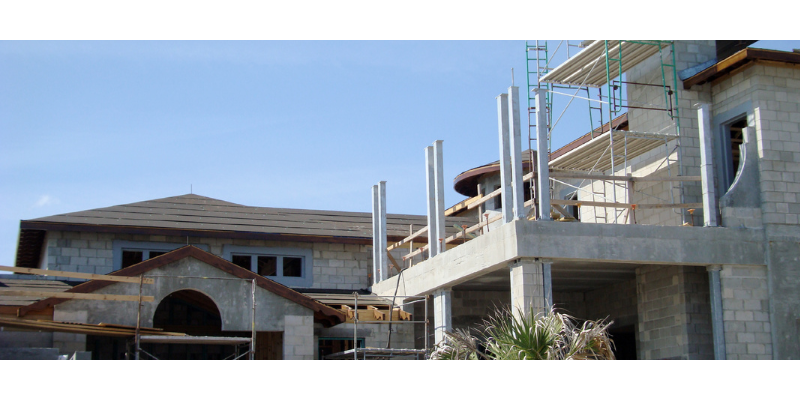
Understanding the Importance of High-Quality Concrete Blocks in Florida Construction
In the unique and often challenging climate of Florida, the choice of construction materials is not just about aesthetics or cost but is deeply rooted in the need for durability, resilience, and long-term performance.
Concrete blocks, as a cornerstone of construction in this region, are particularly valued for their robustness against the diverse and sometimes harsh Floridian weather conditions.
High-quality concrete blocks provide critical resistance to moisture and mold, which are prevalent concerns given Florida’s high humidity and frequent rainfalls.
Additionally, their inherent strength and stability play a pivotal role in safeguarding structures against the high winds of tropical storms and hurricanes that frequently visit the state.
Equally important is the thermal efficiency of high-grade concrete blocks. In a state known for its warm climate, the ability of these blocks to maintain cooler interior temperatures naturally is a significant advantage.
This not only contributes to the comfort and well-being of the occupants but also translates into lower energy consumption and costs, aligning with the growing demand for more sustainable and cost-effective building practices.
Moreover, the versatility of concrete blocks in terms of design and functionality allows contractors to meet various architectural requirements without compromising on safety or quality.
Whether it’s constructing residential homes, commercial buildings, or infrastructural projects, the use of high-quality concrete blocks ensures that these structures stand the test of time, providing security and peace of mind to both builders and occupants.
Thus, understanding and prioritizing the procurement of superior concrete blocks is fundamental for Florida contractors aiming to deliver projects that excel in safety, sustainability, and satisfaction.
The Challenge of Finding Reliable Concrete Block Suppliers for Florida Contractors
Identifying and partnering with dependable concrete block suppliers is a significant hurdle that Florida contractors frequently encounter.
The vast array of suppliers in the market complicates this task, presenting a dilemma in discerning which ones genuinely offer the consistency in quality and reliability in delivery necessary for the seamless execution of construction projects.
This challenge is not merely about sifting through a crowded market but involves delving into the specifics of each supplier’s track record, their adherence to quality standards, and their ability to fulfill orders within the stipulated timelines.
The fluctuating nature of construction demands in Florida, coupled with the logistical complexities of transporting concrete blocks, adds another layer of difficulty.
Suppliers must be capable of scaling their operations to meet large orders for extensive projects while maintaining the integrity of their supply chain to prevent delays.
The unpredictability of weather conditions in the region further exacerbates this challenge, necessitating suppliers that are adept at navigating these hurdles to ensure consistent supply.
Moreover, the quest for suppliers of high-quality concrete blocks that align with the growing demand for sustainable and eco-friendly construction materials in Florida, poses an additional criterion that contractors must consider.
This requires a thorough vetting process, extending beyond conventional metrics of cost and convenience, to include environmental stewardship in their selection criteria.
Consequently, the endeavor to find a concrete block supplier transforms into a multifaceted challenge, demanding diligence, foresight, and a keen eye for quality and sustainability in equal measure.
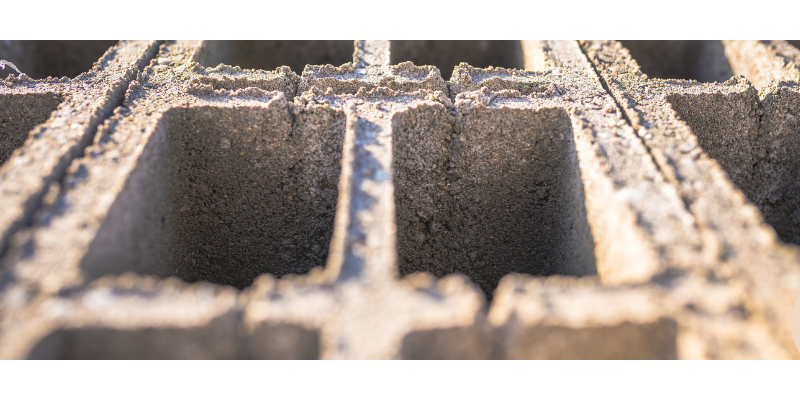
Criteria for Choosing the Right Concrete Block Supplier For Florida Contractors
When embarking on the selection process for construction materials, such as aggregate material, cement, or concrete blocks, it’s imperative to scrutinize a range of critical factors to ensure your construction projects meet the highest standards of quality and efficiency.
First and foremost, the supplier’s reputation within the industry speaks volumes about their reliability and the consistency of their product quality.
Seek out suppliers who have established a strong track record of fulfilling their commitments and maintaining high standards over time.
Experience in the field is another crucial consideration.
Suppliers with extensive experience are more likely to understand the complexities and demands of large-scale construction projects, enabling them to offer valuable insights and tailored solutions to meet your specific needs.
They are also better equipped to navigate the logistical challenges that can arise, ensuring timely delivery of materials.
The quality of the concrete blocks themselves cannot be overstated.
It’s essential to assess the strength, durability, and compliance with industry standards of the supplier’s products.
Requesting samples or visiting existing projects where their blocks have been used can provide a concrete basis for evaluation.
Delivery capabilities are equally important.
A supplier’s ability to fulfill orders promptly and accommodate the scale of your projects without compromising on quality is a vital factor in maintaining project timelines and budgets.
Lastly, exceptional customer service can significantly enhance the supplier-contractor relationship.
Suppliers who are responsive, transparent, and willing to go the extra mile to support your project’s success can be invaluable partners in the construction process.
By carefully considering these criteria, contractors can forge productive partnerships with concrete block suppliers that contribute to the smooth execution and outstanding results of their projects.
The Role of Technology in Streamlining Supply Chain
In the modern construction landscape, the integration of technology into the supply chain has become an indispensable tool for enhancing efficiency and reliability.
For concrete block suppliers for Florida contractors, this means leveraging advanced systems and software to refine production processes, inventory management, and delivery schedules.
Digital platforms enable seamless communication between suppliers and contractors, allowing for real-time updates on order statuses, material availability, and potential delays.
GPS tracking of shipments ensures transparency, providing contractors with up-to-the-minute information on the whereabouts of their orders, significantly reducing the guesswork and anxiety associated with material procurement timelines.
Additionally, predictive analytics can forecast demand surges, enabling suppliers to adjust production in advance and prevent shortages.
By utilizing technology to foster a more cohesive and responsive supply chain, concrete block suppliers can better meet the dynamic needs of Florida contractors, ensuring projects progress smoothly and efficiently, without unnecessary interruptions or delays.
Sustainable and Eco-Friendly Concrete Block Options
As the construction industry continues to pivot towards more sustainable practices, the demand for eco-friendly concrete block options has significantly increased.
Concrete block suppliers for Florida contractors are responding to this shift by innovating and offering products that are not only environmentally responsible but also meet the rigorous demands of the Sunshine State’s construction standards.
These sustainable options often incorporate recycled materials or are produced using less energy-intensive processes, thereby reducing their carbon footprint.
Suppliers are now more focused on minimizing waste during production and exploring the use of renewable energy sources to power their operations.
Some have introduced blocks that support better insulation properties, contributing to the energy efficiency of buildings and helping contractors meet green building certifications such as LEED (Leadership in Energy and Environmental Design).
Additionally, water usage during manufacturing is being optimized to lessen the overall environmental impact.
The use of these eco-friendly concrete blocks does not compromise on quality or durability; rather, they provide added value by enhancing a project’s sustainability credentials.
Contractors have the opportunity to differentiate their offerings and appeal to a market that increasingly values environmental stewardship.
By selecting suppliers that prioritize sustainability, contractors can contribute to a healthier environment while also adhering to the high standards of construction required in Florida.
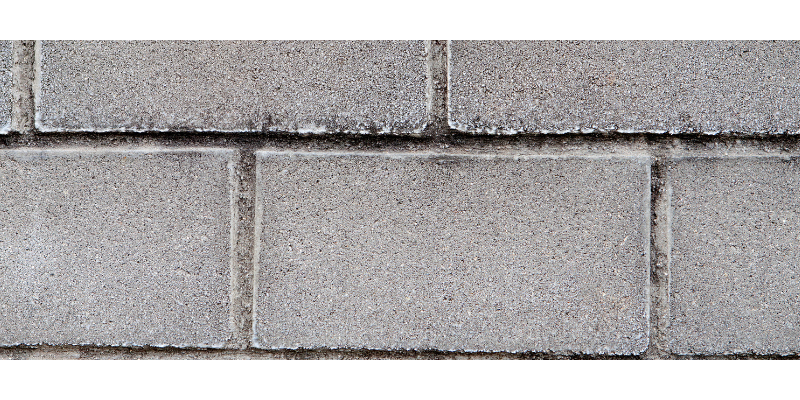
How to Foster Strong Relationships with Suppliers
Fostering strong relationships with concrete block suppliers hinges on consistent, open communication and a foundation of trust and mutual benefit.
It begins with clearly outlining project needs, timelines, and expectations right from the start.
Regular check-ins can keep both parties informed of any project changes or updates, ensuring that any challenges are addressed promptly and collaboratively.
Acknowledging the supplier’s expertise and incorporating their input into project planning can not only lead to more efficient outcomes but also bolster the relationship by valuing their contribution.
Additionally, fair and timely payments for deliveries signal respect for their work and solidify a positive working relationship.
Offering feedback, both positive and constructive, can also guide suppliers in tailoring their services to better meet your needs over time.
When obstacles arise, approaching them with a problem-solving mindset, rather than assigning blame, can help maintain a strong partnership.
Through these practices, contractors can build lasting relationships with suppliers, characterized by reliability and mutual support, which are essential for the timely and successful completion of construction projects.
Case Studies: Successful Florida Projects Using Local Concrete Block Suppliers
Delving into the narratives of successful Florida projects leveraging local concrete block suppliers offers a glimpse into the practical application of strategic supplier selection and the tangible benefits it brings to construction ventures.
One notable example involves a large-scale residential development in South Florida, where the contractor emphasized early engagement with a locally renowned concrete block supplier.
This proactive approach facilitated a tailored production schedule, ensuring the seamless availability of high-quality blocks designed to withstand the state’s humid climate and occasional severe weather conditions.
The project not only met its completion deadline ahead of schedule but also achieved commendable energy efficiency ratings, attributing much of its success to the superior thermal properties of the sourced concrete blocks.
Another case study highlights a commercial construction project in the heart of Orlando that faced stringent architectural demands.
The contractor, in collaboration with Carolina Block Co, a Central Florida masonry store, navigated these challenges by utilizing a variety of specially designed concrete blocks that contributed to the aesthetic appeal and structural integrity of the building.
The partnership allowed for a flexible supply chain that could quickly adapt to design changes without sacrificing project timelines.
These examples underscore the critical role that strong partnerships with local concrete block suppliers play in overcoming project challenges, meeting stringent regulatory standards, and achieving sustainability goals.
They exemplify how strategic supplier relationships not only enhance project outcomes but also contribute to the broader success and resilience of the construction sector in Florida.
Navigating Price Fluctuations and Budget Considerations
In the dynamic landscape of construction, dealing with price fluctuations presents a considerable challenge that directly affects project budgets and financial planning.
Effective collaboration with concrete block suppliers is paramount to mitigate the impact of these changes.
Contractors should engage in transparent discussions with suppliers to gain insights into market trends that may influence prices.
Establishing agreements that offer some level of price stability or flexibility can be a strategic move.
Consider negotiating contracts that include clauses for maximum price variations, which can provide a safeguard against unexpected surges in costs.
Additionally, exploring bulk purchasing or long-term procurement arrangements may yield cost benefits and contribute to budget predictability.
Such strategies can not only secure favorable pricing but also ensure a steady supply of materials, reducing the risk of project delays due to shortages.
Staying abreast of market conditions and fostering open lines of communication with suppliers allows for proactive adjustments to procurement strategies.
By anticipating and planning for potential price movements, contractors can better manage budgets, maintaining project viability even in the face of fluctuating costs.
This approach requires a balance between cost-effectiveness and the need for high-quality concrete blocks, underscoring the importance of strategic supplier partnerships in achieving project success.
Future Trends in Concrete Block Supply for Florida Contractors
The landscape of concrete block supply is poised for significant transformation, shaped by the integration of cutting-edge technologies and a deeper commitment to environmental sustainability.
Innovations such as blockchain for enhanced supply chain transparency, 3D printing for custom block designs, and the utilization of AI for optimizing logistics and production efficiency are on the horizon.
These technological advancements promise to streamline operations, reduce waste, and offer unprecedented flexibility in meeting project specifications.
Simultaneously, the push towards sustainable construction practices is driving the development of new concrete block materials that reduce environmental impact without compromising strength or durability.
This includes the incorporation of recycled materials and the exploration of novel, eco-friendly binders that promise to lower carbon emissions.
Legislative changes aimed at promoting greener building practices will further guide the evolution of concrete block supplies, ensuring that contractors have access to materials that not only meet current standards but also anticipate future regulatory shifts.
As these trends converge, Florida contractors can expect a dynamic and responsive supply market that supports both innovation and sustainability, ensuring that the state’s construction industry remains at the forefront of quality and environmental stewardship.